Nearly half of all visitors to Las Vegas arrive by air at McCarran International Airport, making it one of the 10 busiest airports in the United States. Airside improvements have enabled the airport to safely handle the growing number of aircraft operations, but the two existing terminals, airport roadway and parking facilities were not able to handle its annual capacity target of 53.6 million passengers.
A $2.4 billion airport construction plan was completed that features a new Terminal 3, the addition of 14 more gates and a new automated people-mover system that connects Terminal 3 with McCarran’s existing Terminal 1 via an underground tunnel, maximising the use of the limited space available on the landlocked site. The project included a 1.8 million sq. ft. (167,225 m2) terminal building on three levels.
The Design
Designed by Pierce, Goodwin, Alexander & Linville, Inc. (PGAL), airport construction plans for Terminal 3 included its own central plant, roadway, parking garage, ticketing counters and baggage claim. Passengers are conveyed in comfort by the underground people-mover system to and from the existing D Gates Concourse of Terminal 1, about 900 feet (274 metres) to the south.
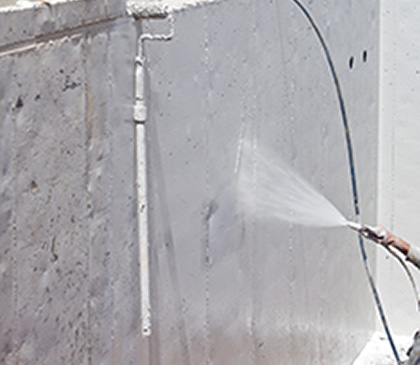
While bustling McCarran International has more than 1,300 slot machines located throughout its existing terminal buildings, the Department of Aviation wasn’t gambling with the Terminal 3 airport construction. Because the train station and utility tunnel were in the water table, waterproofing was critical. The materials specified provided trouble-free resistance to hydrostatic pressure from the groundwater—and had to be installed during cold and severely hot weather.
In addition, notes David Moss, a PGAL Principal, “Aircraft will be parking directly above the train station and the tunnel and it was very critical that the waterproofing system withstand water and also hydrocarbons that may leak from the ramp”.
No Gambling with Airport Construction
As Randall Walker, Director of Aviation at McCarran, sums up: “The airport continues to be a reflection of the community's growth. As the gateway for one of the world's most popular travel destinations, we wanted to ensure we achieve that objective by building and maintaining state-of-the-art facilities, maximising existing resources, and capitalising on new and innovative technology”.
Leveraging GCP’s years of experience in urban project planning, Moss chose to use PREPRUFE® pre-applied waterproofing system, BITUTHENE® self-adhesive membrane waterproofing and HYDRODUCT® drainage composite systems. They are “tested and proven products” that were used in an existing tunnel to the D Gates.
“The previous use of similar GCP products met the owner’s expectations, and their comfort level with this high-performing compatible waterproofing system was another consideration”. he said.
In addition, GCP also provided single-source warranty responsibility for the specified products. The specifications include 3rd party inspection and a 10-year warranty post airport construction.
Airport Construction
Together, the station and the tunnel comprise about 600,000 square feet (55,741 m2) of excavation and airport construction, requiring 275,000 sq. ft. (25,548 m2) of PREPRUFE® and 370,000 sq. ft. (34,374 m2) of BITUTHENE® waterproofing membranes along with HYDRODUCT® drainage composite.
Subsequent stages—the terminal building foundation, central plant-utility tunnel package and roadway package require 612,000 sq. ft. (56,856 m2) of PREPRUFE® and 71,000 sq. ft. (6596 m2) of BITUTHENE® membranes. After excavation, a mud slab, or raft, about 2 inches (5.08 cm) thick was poured to provide a smooth, level subsurface for the underground floor slab. Then PREPRUFE® 300R membrane, specifically designed for use below slabs, was installed. It’s a 46 mm thick membrane with high tensile strength, puncture-resistant HDPE film, and GCP’s patented ADVANCED BOND TECHNOLOGY™.
Blue360sm Product Performance Advantage: Because every project, large or small, deserves the best level of protection.
About PREPRUFE®
PREPRUFE® forms a permanent, seamless seal against water, unlike conventional non-adhering membranes, which cannot prevent water ingress between the membrane and the concrete structure. PREPRUFE®'s high tensile strength withstands the stress of ground settlement.
Shelly Hayden, the Manager of Airport Architecture for the Department of Aviation reported: “Other products don’t compare to PREPRUFE® pre-applied waterproofing system”.
A total of 887,000 sq. ft. (82,404 m2) of PREPRUFE® and 441,000 sq. ft. (40,970 m2) of BITUTHENE® waterproofing membranes along with HYDRODUCT® drainage composite protect the new terminal building, underground ATS tunnel and station, central plant and utility tunnel from groundwater and hydrocarbon runoff from aircraft operations.
gcpat.hk | For technical information: enquiry.hk@gcpat.com
GCP Applied Technologies Inc., 2325 Lakeview Parkway, Alpharetta, GA 30009, USA
GCP (Hong Kong) Ltd., 6 On Chuen Street, On Lok Tsuen Ind Area, Fanling, Hong Kong
This document is only current as of the last updated date stated below and is valid only for use in Hong Kong. It is important that you always refer to the currently available information at the URL below to provide the most current product information at the time of use. Additional literature such as Contractor Manuals, Technical Bulletins, Detail Drawings and detailing recommendations and other relevant documents are also available on www.gcpat.hk. Information found on other websites must not be relied upon, as they may not be up-to-date or applicable to the conditions in your location and we do not accept any responsibility for their content. If there are any conflicts or if you need more information, please contact GCP Customer Service.
Last Updated: 2025-07-21
https://gcpat.hk/en-gb/about/project-profiles/las-vegas-airport-success-after-utilizing-three-gcp-waterproofing-solutions