Commercial roof repair basics: What type of waterproofing is best?
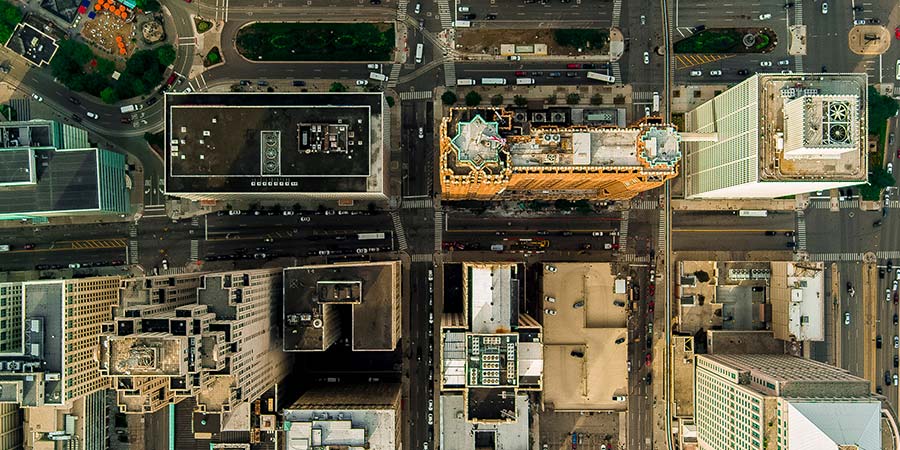
Quickly tackling roof repairs can minimise costly damage, but it’s important to determine the best way to refurbish the roof to help extend the life of the structure. There are a number of factors to consider before deciding how to handle roof repairs.
How much moisture is acceptable for the structure?
For example, if it’s a rooftop of a car park, a little moisture is generally fine. However, other structures such as hospitals, office buildings, and museums must stay completely dry. Many regions have written guidance (ex: British Standard) to help you determine how watertight your roof needs to be.
What is the purpose of the roof?
If you have a roof that’s regularly accessed (such as a green roof or a rooftop car park), it’s important that the waterproofing membrane be durable enough to not only withstand the elements but a high amount of traffic from people and/or vehicles.
What is the extent of the roof damage?
Have a contractor investigate to see if the leak is isolated to one area. If so, you may be able to just patch it instead of undertaking extensive repair work. If the leaks are widespread or difficult to trace, the contractor may need to examine if the current waterproofing is irreparably damaged or whether it can be retained. Depending on the final decision to keep or remove the existing waterproofing, the compatibility of the new waterproofing membrane with the existing membrane needs to be considered.
Consider the schedule
The amount of time available for roof repair – as well as the budget – may dictate the type of waterproofing solution used. For example, if removal of the existing waterproofing is an absolute must, this can take additional time. Often using a fast curing liquid waterproofing solution is best in these situations to help keep the project on schedule.
Are there uneven surfaces to contend with?
Sometimes roofs will wear unevenly due to various circumstances. For example, if one part of the roof is exposed to full sun, it may become worn quicker than areas that are shaded. Often in these cases, liquid waterproofing with a topcoat is a good solution, since it can be applied to uneven surfaces.
What is the roof substrate made of and what condition is it in?
There are different waterproofing systems available to suit various conditions. For example, for a high moisture substrate, epoxy primer is needed, while on a normal substrate, polyurethane primer works well. Your contractor will also need to understand what substrate preparation is needed before re-roofing, e.g. Is a specific primer or sand blasting required for the waterproofing system they choose, in order for it to bond well with the substrate? Is joint treatment required on the construction joint or metal joint?
How often is roof maintenance conducted?
For example, some public housing contracts require that roof maintenance be performed every five years, regardless of what condition the roof is in. Contract terms like this will dictate how long your waterproofing solution needs to last.
Contact a waterproofing specialist
How large is the area to be waterproofed?
If you’re waterproofing a large area and have the ability to do so, you may want to consider using spray-applied liquid waterproofing since it can usually be applied much faster than sheet applied or hand applied solutions. However, if you’re waterproofing a smaller area, have space constraints, weight constraints on the roof that would make it difficult to use a spray machine, or if there are a lot of piping or other structures on the roof, using hand applied liquid waterproofing may be easier.
Tags
- Architects
- Building Envelope Solutions
- Commercial buildings
- Contractor
- Developer
- Distributor
- Engineer
- Owner
- Residential buildings
- Retail buildings
- Silcor®
- Subcontractor
- Waterproofing